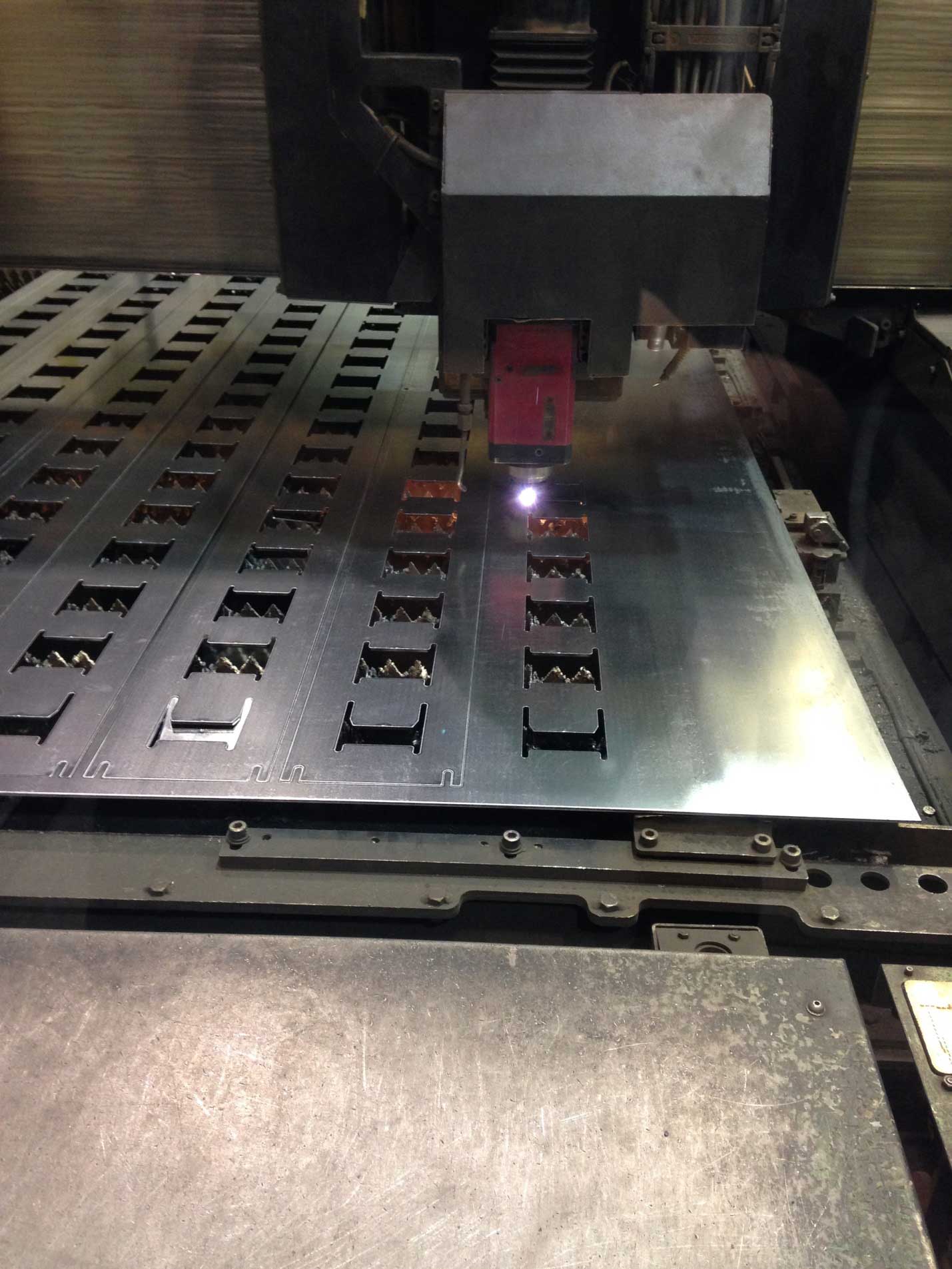
28 Feb Laser Cutting | MetalWorking Group
A common and value-added operation performed by many custom sheet metal fabricators is laser cutting of metals. It is such a common operation that it is hard to believe that very few shops did this 20 years ago.
Technology had to advance in order to make the machines capable of cutting thicker metals, more reliably, and within a reasonable budget compared to other options. “Laser” is actually an acronym for “light amplification by the stimulated emission of radiation”. This is quite a mouthful and it just starts to touch on the technological advances needed to bring laser processes to metal fabrication companies.
In simple terms, the laser machine acts like a giant magnifying glass to concentrate the light energy into a powerful and narrow beam. A good visual is using a magnifying glass concentrating sunlight to burn paper. In an industrial laser, a sophisticated receives electrical power to create a laser beam. Most lasers use a series of advanced optical lenses that bend the bend throughout the machine tool to deliver the concentrated beam to the cutting surface. Newer lasers actually use fiber optics to deliver the energy beam.
Once the beam is concentrated, it can reach tremendous energy levels. Common laser cutting wattages range from 4,000 to 6,000 watts with the capability to cut over an inch thick of steel plate. Some reflective material, such as copper and aluminum, are not conducive to laser cutting as the material tends to reflect some of the power and not absorb it into the cutting function.
The Metalworking Group utilizes a number of lasers to process custom sheet metal fabrications. The laser cut pieces have advantages over traditional punching since there is not a burr with laser cutting. MWG utilizes the lasers to produce large fabrications and parts for production welding.
Below is a picture of a laser operation: